
|
 |
|
Last Updated: Aug 28th, 2006 - 01:36:21 |
2006 CADILLAC STS-V:
CHASSIS Ready for the Track of Autobahn
Performance Division-Tuned Suspension
Re-Tuned ZF Steering Gear
Larger Wheels, Tires, Brakes
Vehicle Launch Control
| DETROIT- While carrying the virtues of sophistication
and elegance expected by today's discriminating high-performance luxury car
buyer - the 2006 Cadillac STS-V has also been developed to be fully capable on
the race track through precision tuning of chassis componentry. True to GM
Performance Division objectives, the STS-V exhibits significant improvements in
forward and lateral acceleration as well as deceleration. Engineers anticipate
zero-to-60 mph times of below 5.0 seconds. All this in a seamlessly integrated
vehicle with abundant, usable low-end torque and a fully automatic
transmission.
Chassis modifications on the STS-V
include:
Vehicle Suspension
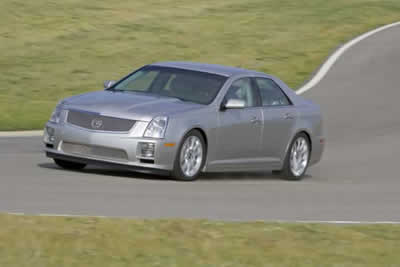 |
STS-V Slicing Through the Corners with Grace and Agility |
To lower the
vehicle's center of mass, engineers lowered the STS-V engine by 14-millimeters
from the base STS V-8 engine position. This change also improved driveline
angles despite shortening of the two-piece prop shaft. The front subframe
required reinforcements optimized for the increased lateral loading to manage
the increased torque of the engine. The rear subframe takes on an even greater
load from torque and cornering. Engineers added mass-optimized reinforcements at
differential mounting points as well as control arm interfaces. An increased
diameter tubular front stabilizer bar (36-mm) coupled with an increase in front
spring rate (75 N/mm) manage the added weight transfer from increased braking
and cornering forces. Correspondingly, the tubular rear stabilizer bar rate was
increased (25.4 mm) to balance vehicle understeer. Rear spring rates (80 N/mm)
were raised to achieve a balanced ride feel. Specifically tuned monotube shock
absorbers manage the increased tire and wheel masses and smooth out road
disturbances. A Nivomat leveling system adjusts ride height with load and
provides increased spring rate and increased damping as the load is increased.
Specific cradle and bushing tuning enhances the smooth transition feel between
moderate and aggressive driving.
Steering A specific, faster
17.2:1 steering gear is included in the chassis tuning package to increase the
steering sensitivity and responsiveness, but by using a ZF variable ratio
steering gear engineers maintained high-speed stability in avoidance situations.
A vehicle-specific steering valve profile effort provides sufficient feedback at
speed while maintaining low parking efforts. Additional changes in profile were
required to balance the more aggressive front tires. A specific high-capacity
steering cooler reduces the potential for loss of system performance during
track operation.
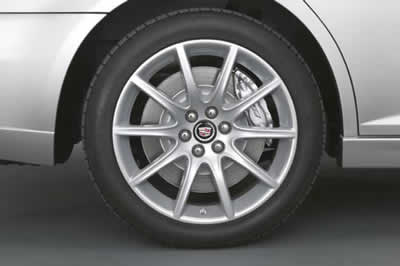 |
The Large Wheels and Brembo Brakes Found on Every Corner of the STS-V |
Tires and
Wheels To connect the power to the ground, the rear tires grew to
P275/40R19 and are mounted on aluminum alloy 9.5-inch wheels. To reduce the
spindle offset on the front steering wheels, and thus improve resistance to
road-induced steer, the front tires are P255/45R18 and mounted on 8.5-inch alloy
wheels. This provides balanced overall vehicle understeer and exceptional
traction to manage the increased power output of the engine. The STS-V rides on
run-flat Extended Mobility Tires (EMT) from Pirelli.
Brakes The
STS-V is equipped with 355-millimeter diameter, 32-millimeter wide vented front
cast iron brake rotors and 365-millimeter diameter, 28-millimeter wide vented
rear cast iron brake rotors supplied by renowned Italian high-performance brake
system manufacturer Brembo. The four-piston calipers feature 77 square
centimeters of pad area on the front, and 51.5 square centimeters of pad area on
the rear caliper. The selection of a specific pad material required balancing of
noise and wear characteristics for both the street and the
circuit.
Chassis Controls The four-channel StabiliTrak chassis
control system has been recalibrated for the vehicle's increase in horsepower
and torque and provides enhanced stability control, especially on
low-coefficient surfaces (i.e. snow or ice). In addition, the system allows the
driver to select from four modes:
Traction and Stability control on;
Traction control off, and Stability control on;
A performance mode, which provides a "less governed" level of stability
control for expert driving
Both Traction and Stability control off.
Vehicle Launch
Control With the increase in torque and the desire to optimize
straight-line performance, a specific combination of traction control, torque
management and driveline disturbance mitigation was required. The unique logic
and prioritizing of system events has led to dramatic improvements in
performance while reducing negative feedback to the driver.This Vehicle Launch
Control feature software tool is a fundamental building block to a refined,
effortless driving experience that has successfully tied together multiple
control systems.
Optimized Engine
Mmounting
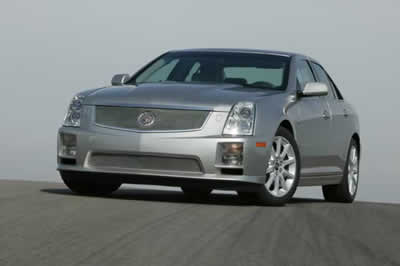 |
The STS-V in its Natural State - On the Track |
With increased engine torque and hotter
thermal environment, the STS-V required engine mounts using EPDM (Ethylene
Propylene Diene Monomer). This special elastomer meets all performance
objectives in a more hostile thermal environment. The mounts have specific
tuning to manage the increased loads imposed by the powertrain while ensuring
the isolation expected in a luxury sedan.
Shock Tower Brace To
enhance steering precision, a tubular structure runs between the shock tower
caps, under the hood and above the engine compartment. The hollow steel brace,
which is a common application in high-performance sports cars, brings superior
cross-vehicle stability to the front of the STS-V as well as enhanced steering
precision and responsiveness.
Discuss this article on AutomotiveForums.com
© Copyright 2006 by AutomotiveArticles.com
Top of Page
|
|
 |
|