
|
 |
|
Last Updated: Aug 28th, 2006 - 01:36:21 |
LS7: THE LARGEST, MOST POWERFUL SMALL-BLOCK EVER BUILT
500 horsepower / 475 lb.-ft. torque
Racing technology transfer takes production engine performance to new heights
Racing-derived CNC-ported aluminum cylinder heads
Each engine assembled by hand by a single, specially-trained builder
| DETROIT - From its inception 50 years ago, GM's small-block V-8 has been a mainstay and favorite of the performance world. Nothing, however, in the production history of this respected eight-cylinder icon comes close to matching the performance of the all-new, 500-horsepower LS7 small-block. GM Powertrain, using valuable data gleaned from the factory-sponsored Corvette C5R racing program, developed the LS7 with many competition-derived components and design features. It takes production small-block performance to an unprecedented level while demonstrating the continuing adaptability of the engine's compact, cam-in-block design. It is, quite simply, the largest, most powerful production small-block V-8 GM has ever produced. The LS7 displaces 7.0 liters - 427 cubic inches - and is standard equipment in the 2006 Corvette Z06. It is identified by red engine covers and is based on the new Gen IV small-block architecture. Unlike the previous Corvette Z06 engine, the LS7 has a separate and distinct engine block casting and reciprocating assembly than the base Corvette engine. And when compared to the LS2, it has a different front cover, oil pan, exhaust manifolds and cylinder heads. The unique block accommodates large-displacement cylinders, while other components make use of racing-derived lightweight components to help boost horsepower and rpm capability.
The LS7's specifications are significant for a production engine:
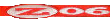 |
500 horsepower @ 6200 rpm |
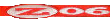 |
475 lb.-ft. of torque @ 4800 rpm |
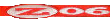 |
7000-rpm redline |
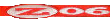 |
Unique engine block with larger 104.8-mm (4.125-inch) bores and pressed-in cylinder liners |
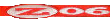 |
Forged steel crankshaft with 101.6-mm (4-inch) stroke |
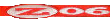 |
Titanium connecting rods |
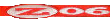 |
Cast aluminum flat-top pistons |
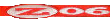 |
Racing-derived CNC-ported aluminum cylinder heads with titanium intake valves and sodium-filled exhaust valves |
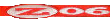 |
Dry-sump oiling system |
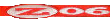 |
11.0:1 compression ratio |
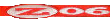 |
Camshaft with 15-mm (.591-inch) lift |
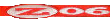 |
Hydroformed exhaust headers with unique "quad flow" collector flanges. | All LS7 engines are assembled by hand at GM's new Performance Build Center in Wixom, Mich. The exacting standards to which they are built include deck-plate boring and honing of the cylinders and even crank line-boring of the block with the deck plates and side bolts installed - procedures normally associated with the building of racing engines and almost unheard of in a production-vehicle engine.
"In many ways, the LS7 is a racing engine in a street car," said Dave Muscaro, assistant chief engineer of small-block V-8 for passenger cars. "We've taken much of what we've learned over the years from the 7.0-liter C5R racing program and instilled it here. There really has been nothing else like it offered in a GM production vehicle."
Indeed, the LS7's engineers spent as much time at racetracks as they did at engine dynamometers. Everything from the cylinder heads to the unique dry-sump oiling system has a direct line back to the racing program. But while the LS7 has racing roots, it delivers its performance with uncompromising smoothness and tractability - qualities that make the Corvette Z06 a daily-driveable supercar.
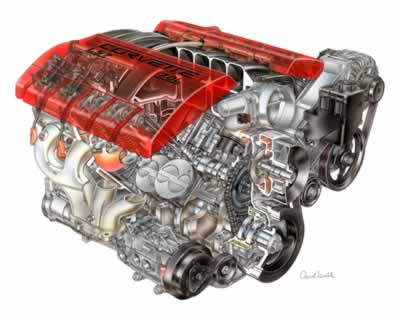 |
Cutaway View of the LS7 Revealing the Internal Structure |
Cylinder Block & Reciprocating Assembly The LS7's competition-proven construction is exemplified in the cylinder block and reciprocating assembly, where an all-new aluminum block casting is used to provide room for its large, 104.8-mm-diameter (4.125-inch) cylinder bores. Inside the cylinders, aluminum flat-top pistons deliver an 11.0:1 compression ratio. They're connected to a precision-balanced forged steel crankshaft with a 101.6-mm (4-inch) stroke via lightweight titanium connecting rods. The titanium rods weigh just 480 grams apiece - almost 30 percent less than the rods in the LS2 V-8. Besides being lightweight, which enhances high-rpm performance and rpm range, titanium makes the rods extremely durable. And as with features like deck-plate honing, the use of premium titanium connecting rods typically is seen only in all-out racing engines. Other details of the cylinder block assembly include pressed-in cylinder sleeves and forged steel main bearing caps. Pressed-in cylinder sleeves are used to allow the large 104.8-mm bore while the six-bolt, doweled-in-place CNC-machined forged steel main caps offer the superior strength required at the LS7's power level. The smaller-displacement LS2 engine (101.6-mm bore x 92-mm stroke) has cast-in cylinder sleeves and powder metal main caps.
Dry Sump Oiling System The LS7 has a dry-sump oiling system designed to keep the engine properly lubricated during the high cornering loads the Corvette Z06 is capable of producing. An engine compartment-mounted 8-quart reservoir delivers oil to the engine oil pump under the demanding conditions of cornering loads in excess of 1 g. Oil circulates through the engine and down to the oil pan, where it is sent back to the reservoir via a scavenge pump. The large-capacity reservoir, combined with a high-efficiency air-to-oil cooler, provides necessary engine oil cooling under the demands of the engine's power output. With the dry-sump system, oil is added to the engine via the reservoir tank - which includes the oil level dipstick. The LS7's dry-sump system was developed and tested on racetracks in the United States and Europe, including Germany's famed Nürburgring. And while common in racing cars, the Corvette Z06 is one of just a handful of production vehicles - and the only production Corvette - to ever incorporate such a high-performance oiling system.
Cylinder Heads The LS7's CNC-ported aluminum cylinder heads are all-new and designed to meet the high airflow demands of the engine's 7.0-liter displacement. Airflow has increased 25 percent compared to the base Corvette's 6.0-liter LS2 V-8. To ensure optimal, uninterrupted airflow, the LS7 has straight, tunnel-like intake runners. Very large by production-vehicle standards, the ports are designed to maintain fast airflow velocity, providing excellent torque at low rpm and exhilarating horsepower at high rpm. Their design is yet another legacy of the Corvette C5R racing program. The heads feature 70-cc combustion chambers that are fed by huge, 56-mm-diameter titanium intake valves. The lightweight titanium valves each weigh 21 grams less than the stainless steel valves used in the LS2, despite the valve head having 22 percent more area. They are complemented by 41-mm sodium-filled exhaust valves (vs. 39.4-mm valves in the LS2). To accommodate the large valve face diameters, the heads' valve seats are siamesed; and, taken from experience with the engines of C5R racecars, the LS7's valve angles are held at 12 degrees - vs. 15 degrees for the LS2 - to enhance airflow through the ports.
"The heads are simply works of mechanical art," said Muscaro. "We left nothing on the table when it came to ensuring the best airflow through the engine."
Complete CNC porting of each cylinder head is performed on state-of-the-art five-axis milling machines, which carve out the intake ports, exhaust ports and combustion chambers with mathematical precision. In comparison, the LS2 features cast aluminum heads that require minimal finishing operations.
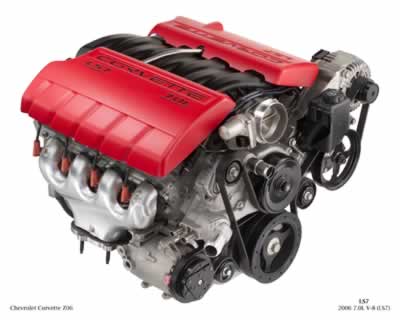 |
Exposed Hydro Formed Exhaust Manifold |
Camshaft, Exhaust & Other Features A unique hydraulic roller camshaft actuates the large valves, giving them the time needed to bring in the air/fuel mixture and clear out the exhaust from the LS7's large air passages. Based on C5R racing experience, the LS7's cam has an all-new profile that provides .591-inch lift (15 mm) on both the intake and exhaust valves - almost .066 inch more than the LS2's already stout .525-inch lift specs. To accommodate the extremely high valve lift and the large ports, 1.8:1 roller rocker arms - offset on the intake side - and raised valve spring seats are used. In contrast, the LS2 has 1.7:1 conventional roller rockers.
Like other Gen IV V-8 engines, the LS7 uses a composite, three-piece friction-welded intake manifold, although its passages are tuned to support the engine's considerable airflow requirements. The manifold is fronted by a 90-mm-diameter single-bore, electronically controlled throttle body. Higher-capacity, five gram/sec fuel injectors also are mounted in the manifold assembly. Like the LS2, the LS7 has a returnless fuel system that enhances both power and emissions performance.
On the exhaust side, racing-style hydroformed steel tubular exhaust headers are used. The individual header tubes meet at a special quad-outlet collector flange at the very tip of the header outlet where they smoothly enter into a "wide-mouth" catalytic converter. This system design approach greatly contributes to the Z06's backpressure. The four rectangular sections of the flange smooth the exhaust flow out of the engine. Hydroformed exhaust headers are unique to the LS7 and are a specialty even among racing engines.
Built By Hand Assembly of every LS7 engine is performed by hand by a dedicated team member at GM's new Performance Build Center. The engines are pushed through approximately 15 sub-assembly stations, where only the components and tools necessary to complete the station's task are on hand. Tools such as electric torque wrenches provide repeatable accuracy for the engine's precise tolerances, while the eyes of the specially trained team members provide intangible attention to detail. Team members are engine-build specialists selected from GM's experimental engine lab, and they complete about 30 LS7 engines per day. Upon completion, each engine is balanced and subjected to a 20-minute heat test. It is then transported to the Corvette Assembly Plant in Bowling Green, Ky., to be married with a new Corvette Z06.
Discuss this article on AutomotiveForums.com
© Copyright 2006 by AutomotiveArticles.com
Top of Page
|
|
 |
|